CPR simulators will give you realistic scenarios to hone life-saving skills. To ensure their optimal performance and longevity, proper maintenance is crucial. Additionally, when the time comes to retire a simulator, it’s essential to dispose of it responsibly and environmentally. This article delves into the best practices for maintaining CPR simulators, from daily care to end-of-life disposal. By following these guidelines, healthcare organizations can maximize the effectiveness of their training equipment and minimize their environmental impact.
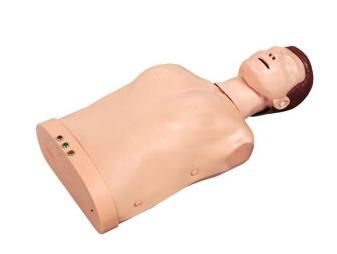
Maintenance Points for CPR Simulators
The maintenance of CPR simulators involves several key aspects:
Daily Use and Operation Precautions
- Gentle handling: Due to the complex internal structure, avoid rough handling of the simulator to prevent damage.
- Keep dry: Ensure the model and server remain dry to prevent short circuits.
- Cleaning: Use a clean, dry cloth to wipe the simulator’s surface. If a cleaner is needed, use a neutral cleaner like plant-based cleaner. Avoid strong acids or bases as they can corrode the material or cause discoloration.
Cleaning and Disinfection
- Disinfection: Clean the simulator’s scalp, mouth, nose, chest skin, and breathing tube with a cleaner and then soak in a disinfectant, such as 75% alcohol.
- Replaceable parts: Regularly inspect and replace parts like the lung bag as needed to ensure optimal performance and accurate feedback.
- UV disinfection: Place the simulator in a storage cabinet for UV disinfection to protect the model from damage.
Electrical Component Maintenance
- Avoid external devices: Prevent using external digital storage devices on the simulator’s computer to reduce the risk of virus transmission.
- Proper power cycle: Strictly follow the power on/off sequence for electronic medical models to protect the electronic components.
Battery Replacement and Maintenance
- Battery indicator: Replace the batteries when the indicator light dims. Replace with two AA batteries.
- Storage: Store the CPR simulator and computer monitor in a well-ventilated, dry place, away from moisture and direct sunlight to extend the device’s lifespan.
Regular Inspection and Functional Testing
- Regular checks: Conduct regular visual and functional inspections to ensure all components are clean, free of contaminants, and have no wear, looseness, or damage.
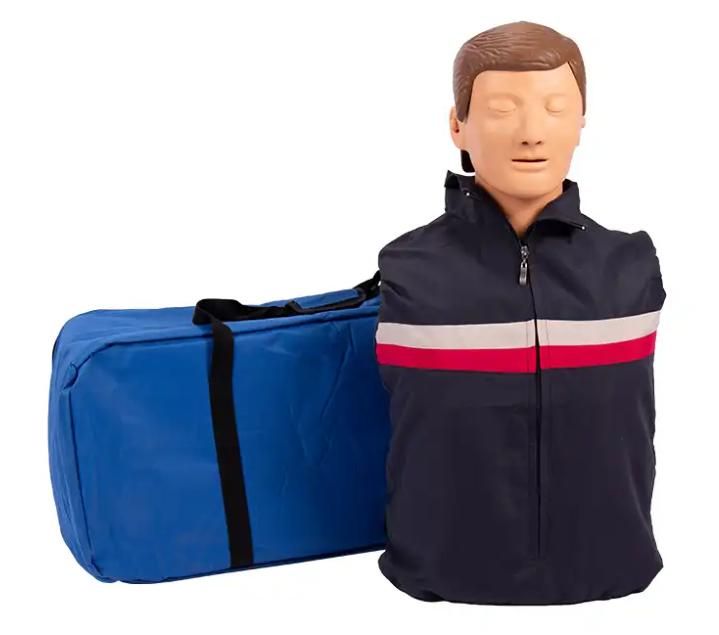
What Factors Should Be Considered When Disposing of CPR Simulators?
- Compliance with Environmental Regulations: Before disposing of a CPR simulator, it’s crucial to understand and comply with local environmental regulations and recycling policies. This includes specific regulations for electronic waste, as simulators often contain batteries and other electronic components.
- Safe Dismantling: Professional dismantling is recommended to ensure the safe handling of hazardous materials. This may involve removing batteries, electronic components, and any potential biohazardous materials.
- Recycling and Reuse: Non-hazardous parts of the simulator, such as plastics and metals, should be recycled whenever possible to minimize environmental impact. Contact local recycling centers or inquire about the manufacturer’s recycling programs.
- Hazardous Material Handling: If the simulator contains hazardous chemicals or heavy metals, it should be disposed of by a qualified waste management company to prevent contamination of soil and water sources.
- Documentation: Maintain records of all waste types, quantities, and disposal methods for tracking and compliance verification.
- Key Considerations: When disposing of CPR simulators, pay particular attention to the proper handling of electronic waste and hazardous materials to protect the environment and public health. If specific disposal guidelines or partner information are available in search results, prioritize these options. If no direct and up-to-date information can be found, consult with a professional waste management company or local environmental protection agency for guidance.
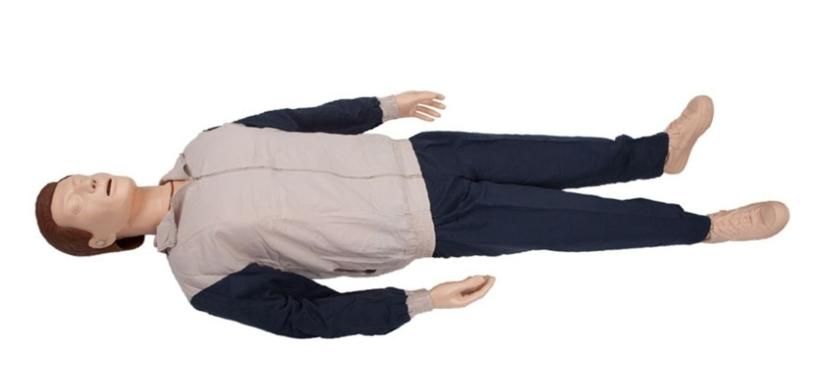
Recycling Options for CPR Simulators
There are several avenues for recycling CPR simulators:
- Manufacturer’s Take-back Programs: Many manufacturers offer product take-back programs. Contact the manufacturer directly to inquire about specific recycling services or recommended recycling channels.
- Medical Equipment Recycling Companies: Specialized medical equipment recycling companies can provide recycling services for a variety of medical devices, including CPR simulators. These companies typically categorize equipment, refurbishing reusable parts and disposing of non-reusable components in an environmentally responsible manner.
- Local Government or Community Recycling Programs: Some local governments or community organizations may have specific recycling programs for collecting and processing medical equipment. Check with your local environmental department or community service center to see if such services are available.
- Electronic Waste Recycling Centers: Since CPR simulators may contain electronic components, they can be disposed of as electronic waste at specialized recycling centers. These centers ensure that hazardous materials are handled appropriately.
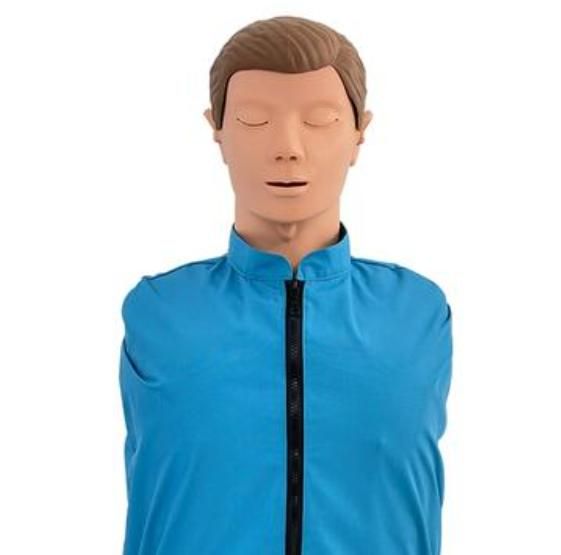
Overview
Adhering to these maintenance practices and responsible disposal methods, healthcare organizations can significantly extend the lifespan of their CPR simulators, ensuring their continued effectiveness in training. Regular inspections, cleaning, and proper storage will help prevent premature wear and tear. When the time comes to retire a simulator, careful consideration of environmental regulations and recycling options! If you want to get more information about CPR simulators, please consult with professional CPR simulator supplier Scopelab.