In the realm of material science and engineering, hardness testing is a pivotal process used to determine the resistance of a material to localized plastic deformation. Two of the most widely recognized hardness testing methods are the Brinell and Rockwell hardness tests.
The choice between Brinell and Rockwell hardness testers is not arbitrary; it depends on the specific characteristics of the material being tested, the accuracy required, and the size and shape of the specimen. This article aims to provide a comprehensive comparison of the Brinell and Rockwell hardness tests, outlining their measurement principles, testing methods, and applications. After understanding these differences, engineers and material scientists can select the appropriate hardness testing method to ensure the reliability and relevance of their test results for quality control, research, and development purposes.

Differences in Measurement Principles
- Brinell Hardness Tester: The Brinell hardness tester employs a diamond indenter that is pressed into the surface of the test specimen. The diameter of the resulting indentation is measured, and the Brinell hardness number is calculated based on the applied load and the diameter of the indentation. The hardness value is influenced by factors such as the diameter of the test ball, the applied load, and the depth of indentation.
- Rockwell Hardness Tester: The Rockwell hardness tester is based on the principle of indentation. A diamond cone or steel ball indenter is pressed into the material with a minor load, followed by a major load. The difference in depth of penetration between the minor and major loads is measured. The Rockwell hardness number is determined based on the depth of penetration and is read directly from a dial.
Differences in Testing Methods
Feature | Brinell Hardness Tester | Rockwell Hardness Tester | Explanation |
Testing Method | Microscopic measurement of indentation diameter | Direct reading from a dial | Brinell requires a microscope for measurement, while Rockwell provides a direct reading. |
Procedure | 1. Apply a major load to the specimen. 2. Measure the diameter of the indentation using a microscope and calibrated scale. | 1. Apply a minor load to the specimen. 2. Apply a major load. 3. Measure the depth of penetration using a dial gauge. | The Brinell test involves a more complex measurement process, while the Rockwell test is simpler and more direct. |
Time Required | Typically longer | Shorter | The Brinell test generally takes more time due to the microscopic measurement and calculations, while the Rockwell test provides a quicker result. |
Operator Skill | Requires skilled operator to accurately measure indentation diameter | Less demanding, but operator still needs to ensure proper alignment and loading | Brinell requires a higher level of skill for accurate measurements, while Rockwell is less demanding but still requires proper technique. |
Accuracy | Can be highly accurate with proper technique and calibration | Generally accurate, but may be influenced by factors like surface finish and specimen thickness | The accuracy of both tests depends on factors like operator skill, calibration, and specimen preparation. |
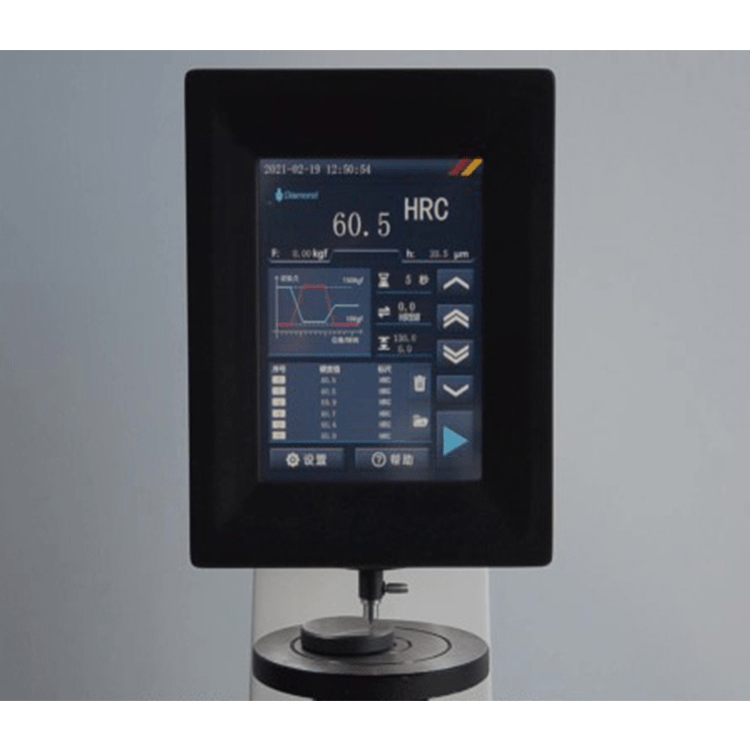
Differences in Applications
Feature | Brinell Hardness Tester | Rockwell Hardness Tester | Explanation |
Suitable Materials | Softer materials, non-ferrous metals, plastics, and thin-walled specimens. | Wide range of materials, including metals, plastics, and ceramics. | Brinell is more suitable for softer materials, while Rockwell can be used for a wider range of materials. |
Advantages for Applications | Accurate for soft materials, provides a large indentation for visual inspection. | Faster, easier to use, suitable for a wide range of materials, smaller indentation. | Brinell offers high accuracy for soft materials, while Rockwell is more convenient and versatile. |
Disadvantages for Applications | Large indentation may damage small specimens. | May not be as accurate for very hard materials. | The Brinell test may not be ideal for testing small parts, while Rockwell may have limitations for very hard materials. |
Common Applications | Quality control, research, and development for soft materials, thin-walled tubes, and small specimens. | Quality control, incoming inspection, and research for a wide range of materials. | Brinell is often used for testing soft materials and thin sections, while Rockwell is widely used in industrial applications. |
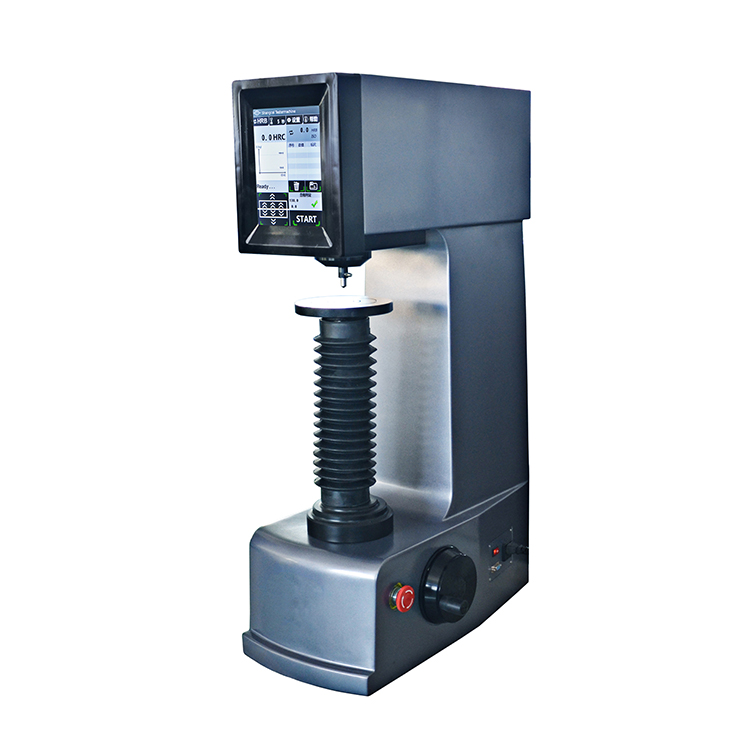
How to Choose Brinell or Rockwell Hardness Testers for My Needs?
The choice between Brinell and Rockwell hardness testers depends on various factors, including the type of material being tested, the desired level of accuracy, and the size and shape of the specimen. Here’s a breakdown to help you make an informed decision:
Material Type
- Soft materials: Brinell is generally more suitable for testing softer materials like non-ferrous metals, plastics, and thin-walled tubes.
- Hard materials: Rockwell is better equipped for testing harder materials, including steels and ceramics.
Accuracy Requirements
- High accuracy: Brinell tests offer higher accuracy for soft materials due to the larger indentation.
- Quick results: Rockwell tests are faster and more convenient for routine testing or when quick results are needed.
Specimen Size and Shape
- Small specimens: Rockwell is often preferred for testing small specimens due to the smaller indentation.
- Thin-walled specimens: Brinell may be more suitable for testing thin-walled tubes due to the larger indentation, which can provide better visibility for measurement.
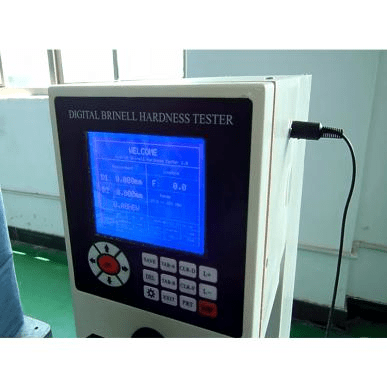
Choose the Right Hardness Tester for Your Needs
The choice of a Brinell or Rockwell hardness tester is determined by the material’s properties, the level of accuracy required, and the physical dimensions of the specimen. Brinell hardness testing is useful for coarse-grained materials and when a larger indentation is required for measurement, whereas Rockwell hardness testing is better suited for fine-grained materials, thin coatings, and applications that require faster testing. Understanding the principles and applications of both methods enables a more informed decision about which hardness tester to use, resulting in more accurate and meaningful hardness data. The choice between Brinell and Rockwell hardness testers is more than just a matter of preference; it is a strategic decision that can affect the quality and performance of materials in a variety of industrial applications.
Suppose you are still unsure which hardness tester to choose, so why not consult the hardness tester supplier Scopelab. As a professional laboratory product supplier, we can provide you with not only high-quality products but also reliable advice.