The Brinell hardness test has been a cornerstone of material evaluation, providing a dependable method for determining a material’s resistance to permanent deformation. However, traditional Brinell testers relied on manual operation and subjective interpretation of indentation marks, which could lead to inconsistencies and human error. The introduction of digital Brinell hardness testers represents a significant advancement in material testing technology. Scopelab investigates the world of digital Brinell hardness testers, highlighting their distinct advantages over traditional methods. We’ll see how they provide exceptional accuracy, versatility, and operational efficiency. In addition, we’ll look at how these testers are used in a variety of industries, emphasizing their importance in ensuring material integrity and quality.
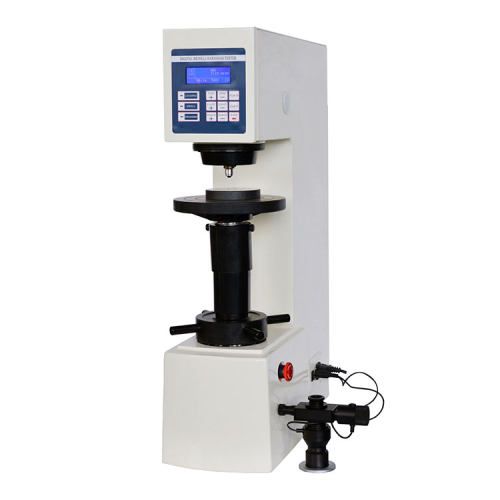
Advantages of Digital Brinell Hardness Tester
Traditional Brinell testers rely heavily on manual operation and subjective interpretation of indentation marks. Digital testers address these limitations by introducing a few key benefits:
- Superior Accuracy: Digital models rely on advanced load cells and sophisticated electronics. This results in high accuracy, typically within ± 3.5% or even better for certain models (XHB-3000). This level of precision ensures that hardness measurements are accurate and consistent across multiple tests.
- Versatility for Diverse Materials: These testers are versatile and can test a variety of materials. They can handle test forces ranging from 62.5 kgf to a substantial 3000 kgf. This enables them to assess the hardness of materials ranging from soft metals such as aluminum to extremely hard alloys used in critical applications.
- Automated Efficiency: Manual test procedures are no longer used. Digital Brinell testers provide an automated testing cycle. This eliminates the possibility of human error and guarantees consistent testing conditions. Automation promotes repeatability and improves the reliability of results.
- Digital Display and Data Management: The digital screen displays the measured hardness value, eliminating the need to manually interpret indentation marks. Many models go a step further by providing data storage capabilities. This allows for simple record-keeping and later analysis of test results.
- User-Friendly Interface: These testers have simple, intuitive interfaces. Even those without a technical background can quickly learn to use them. This user-friendliness shortens training time and improves the overall testing process.
- Built for Endurance: Digital Brinell testers are designed for durability. Their tough design enables them to withstand the harsh conditions commonly found in industrial settings. This guarantees long-term performance and dependable operation for years to come.
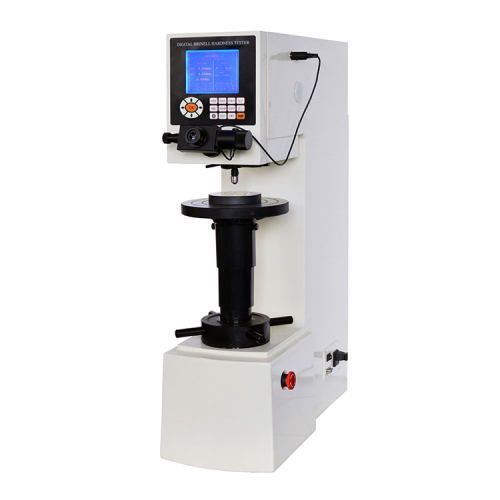
Applications of Digital Brinell Hardness Testers
Because of their unique capabilities, digital Brinell hardness testers are an extremely useful tool in a variety of industries. Let’s dig deeper into how these testers help specific industries:
1. Metalworking
- Quality Control: In metalworking, maintaining consistent material properties is critical. Brinell hardness testing enables manufacturers to ensure that their metals (steel, aluminum, and copper alloys) meet the necessary hardness requirements. This aids in detecting any inconsistencies or flaws that may jeopardize the final product’s performance or safety.
- Material Selection: Metal types have different hardness ranges. Brinell testers assist manufacturers in selecting the most appropriate material for a given application. For example, gears require a harder metal than decorative trims. Accurate hardness measurements prevent the use of incorrect materials, saving time, resources, and potential product failures.
- Heat Treatment Optimization: Heat treatments such as annealing, hardening, and tempering significantly impact a metal’s hardness. Brinell testers enable manufacturers to monitor hardness changes caused by heat treatment and fine-tune process parameters. This ensures they reach the desired final hardness for peak performance.
2. Automotive Industry
- Strength and Durability of Critical Components: Vehicle safety and functionality depend on component strength and durability. Gears, bearings, and engine components are subjected to extreme pressure and wear. Brinell hardness testing allows manufacturers to ensure that their components meet the required hardness specifications. This lowers the likelihood of failures and accidents on the road.
- Material Selection for Specific Parts: Different automotive components require varying degrees of hardness. For example, crankshafts must be extremely hard to withstand engine torque, whereas suspension components may require a balance of hardness and flexibility. Brinell testers recommend materials based on the specific requirements of each component.
3. Aerospace Materials
- Structural Integrity of Aircraft Components: Aircraft structures are subjected to tremendous forces while in flight. To ensure safety, aerospace manufacturers use Brinell hardness testing to assess the materials used in wings, fuselages, and landing gear. This testing ensures that the materials have the required hardness to withstand these stresses while maintaining structural integrity.
- Material Qualification for Flight Safety: The materials used in aircraft construction are subject to strict regulations. Brinell hardness testing is an important part of material qualification processes. It ensures that the materials meet the hardness requirements established by regulatory bodies, ensuring the safety of passengers and crew.
4. Tool and Die Manufacturing
- Assessing Tool and Die Hardness: Tool and die effectiveness is determined by their durability during metal forming operations. Brinell hardness testers help manufacturers determine the hardness of their tools and dies. This ensures that they have the strength to hold their shape, reduce wear, and consistently produce high-quality parts.
- Optimizing Tool Life: Monitoring hardness changes in tools and dies over time allows manufacturers to predict and address wear before it impacts production. This enables them to maximize tool life and schedule timely replacements, reducing downtime and production costs.
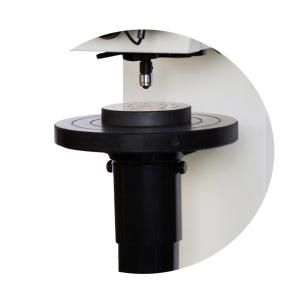
Digital Brinell Hardness Testers Provided by Scopelab
MHB-3000 Digital Brinell Hardness Tester | XHB-3000 Digital Brinell Hardness Tester | |
Test Force | 612.9N, 980.7N, 1226N, 1839N, 2452N, 4903N, 7355N, 9807N, 14710N, 29420N | 612.9N, 980.7N, 1226N, 1839N, 2452N, 4903N, 7355N, 9807N, 14710N, 29420N |
Test Range | 3.18~653HBW | 3.18~653HBW |
Hardness Reading | LCD Display | LCD Display |
Microscope | 20× Digital Measuring Microscope | 20× Digital Measuring Eyepiece, 1× Objective |
Effective Field of View | 6mm | 6mm |
Min. Measuring Unit | 0.001mm | 0.001mm |
Dwell Time | 0~60s | 0~60s |
Max. Sample Height | 205mm | 215mm |
Throat Depth | 135mm | 135mm |
Power Supply | AC220V, 50Hz | AC220V, 50Hz |
Execute Standard | ISO 6506, ASTM E10, JIS Z2243, GB/T 231.2 | ISO 6506, ASTM E10, JIS Z2243, GB/T 231.2 |
Dimension | 545×235×755mm, Packing Dimension: 650×435×1020mm | 545×235×790mm, Packing Dimension: 650×435×1060mm |
Weight | Net Weight: 130kg, Gross Weight: 160kg | Net Weight: 130kg, Gross Weight: 160kg |
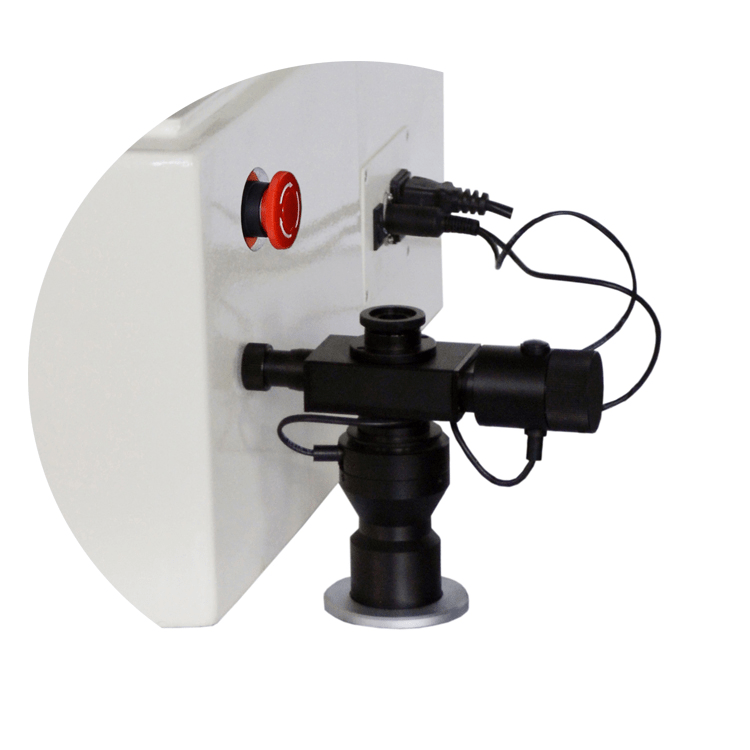
Conclusion
Digital Brinell hardness testers have transformed the field of material testing. They provide unparalleled accuracy, a broader testing range, and streamlined testing procedures by combining advanced technology and automation. These advancements result in numerous benefits for a variety of industries. Digital Brinell hardness testers help to maintain quality standards by ensuring the strength and durability of critical automotive components and optimizing heat treatment processes in metalworking. As industries strive for continuous improvement, these sophisticated testers will unquestionably remain an important tool for material evaluation and process control.