Metallographic polishing machines are indispensable tools for preparing metal samples for microscopic examination. By creating smooth, flat surfaces, these machines enable researchers and engineers to analyze the microstructure of metals and alloys, revealing critical information about their composition, properties, and defects. There is a guide that explores the various types of metallographic polishing machines, their working principles, and their wide-ranging applications in fields such as material science, metallurgy, quality control, and research and development.
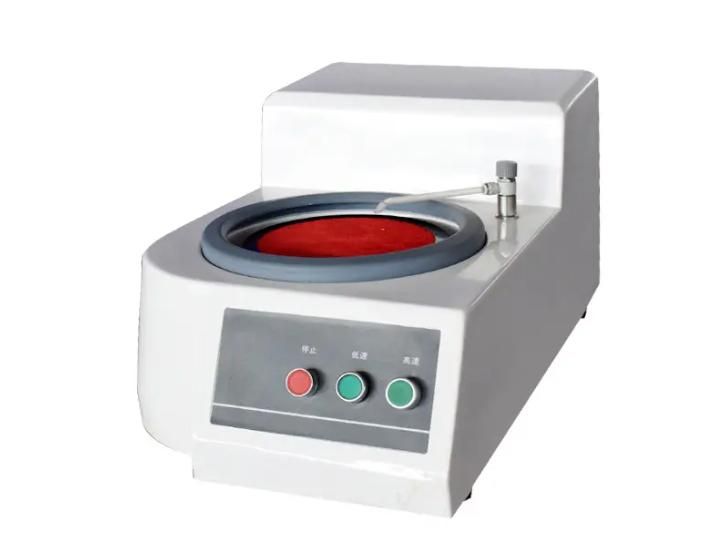
Metallographic Polishing Machines Working Principle
Metallographic polishing machines are essential tools for preparing metal samples for microscopic examination. They are used to create a smooth, flat surface on the metal specimen, free from scratches or other imperfections that could interfere with the analysis. The basic working principle of a metallographic polishing machine involves the use of abrasive materials to remove material from the metal surface. These abrasive materials can be in the form of powders, slurries, or lapping films. The machine typically consists of a rotating platen or wheel that is covered with abrasive material. The metal sample is pressed against the platen, and as it rotates, the abrasive material removes material from the surface.
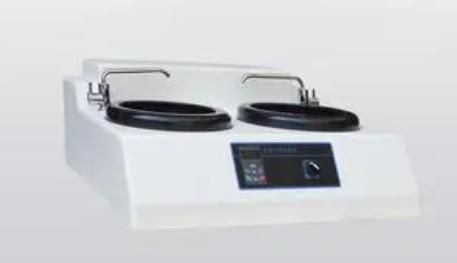
Types of Metallographic Polishing Machines
Metallographic polishing machines come in various configurations, each designed to meet specific needs and preferences. Here are some of the most common types:
Description | Advantages | Examples | |
Single Wheel Polishing Machine | A single wheel polishing machine features a single rotating platen or wheel that is covered with abrasive material. The metal sample is pressed against the platen, and as it rotates, the abrasive material removes material from the surface. | Simple design, easy to operate, and relatively affordable. Suitable for smaller laboratories or occasional polishing tasks. | YMP-1 Metallographic Sample Grinding and Polishing Machine |
Dual Wheel Polishing Machine | A dual wheel polishing machine has two rotating platens or wheels, allowing for a more efficient and consistent polishing process. The metal sample can be moved between the two wheels, using different abrasive materials or pressures for each stage of the polishing process. | Improved efficiency and consistency compared to single wheel machines. Can handle larger and more complex samples. | YMP-2 Metallographic Sample Grinding and Polishing Machine |
Semi-Automatic Polishing Machine | A semi-automatic polishing machine incorporates some automated features, such as automatic pressure application or sample movement. However, it still requires manual operation for certain tasks, such as loading and unloading the sample. | Combines the benefits of manual and automatic polishing, offering a balance of control and efficiency. Suitable for laboratories that require both manual flexibility and automated assistance. | |
Automatic Polishing Machine | An automatic polishing machine is fully automated, capable of performing the entire polishing process with minimal human intervention. These machines often feature programmable controls, allowing for precise control over polishing parameters such as pressure, speed, and time. | Highest level of efficiency and consistency. Ideal for high-volume or critical applications where precision and repeatability are essential. | YMPZ-1 Automatic Metallographic Sample Grinding and Polishing Machine |
The choice of metallographic polishing machine will depend on factors such as the volume of samples, the desired level of automation, and the specific requirements of the application. By understanding the different types of machines and their advantages and disadvantages, you can select the most suitable option for your laboratory’s needs.
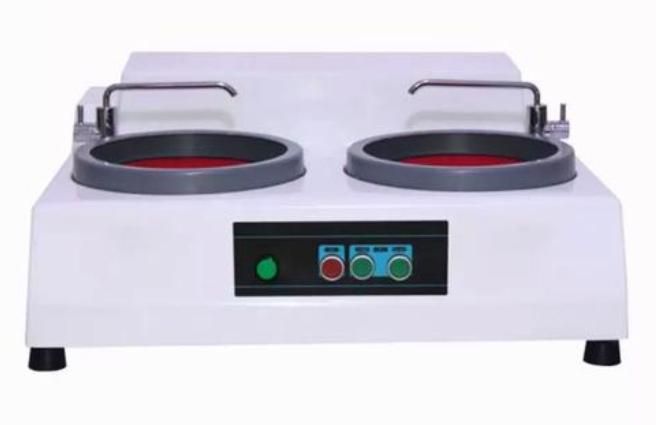
Applications of Metallographic Polishing Machines
Metallographic polishing machines play a crucial role in various scientific and industrial fields, enabling detailed analysis of the microstructure of metals and alloys. By preparing smooth, flat surfaces on metal samples, these machines facilitate microscopic examination, revealing essential information about the material’s composition, grain size, defects, and processing history.
Material Science
- Microstructure analysis: Metallographic polishing is essential for studying the microstructure of materials, including grain size, shape, and orientation. This information is crucial for understanding the material’s properties and behavior.
- Phase identification: By using different etchants, metallographers can reveal the presence of various phases within a material, such as different alloys or precipitates. This is valuable for understanding phase transformations and the effects of heat treatment.
- Defect analysis: Metallographic polishing can reveal defects such as cracks, inclusions, and porosity, which can impact the material’s strength, ductility, and overall performance.
Metallurgy
- Alloy development: Metallographers use polishing techniques to study the microstructure of new alloys and evaluate their properties. This information is essential for developing alloys with specific characteristics, such as high strength, corrosion resistance, or wear resistance.
- Heat treatment studies: Metallographic polishing is used to examine the effects of heat treatment processes on the microstructure of metals. This information is crucial for optimizing heat treatment cycles to achieve desired properties.
- Failure analysis: By examining the microstructure of failed components, metallographers can determine the root cause of failure, such as fatigue, corrosion, or improper heat treatment.
Quality Control
- Incoming inspection: Metallographic polishing is used to verify the quality of incoming materials, ensuring they meet specified standards.
- Process monitoring: Metallographic analysis can be used to monitor the quality of manufacturing processes, such as welding, casting, and heat treatment.
- Non-destructive testing: While metallographic examination requires sample preparation, it can be considered a non-destructive testing method when only a small portion of the material is removed.
Research and Development
- New materials development: Metallographic polishing is essential for characterizing new materials, such as advanced alloys, composites, and coatings.
- Fundamental research: Metallographers contribute to fundamental research in materials science by studying the relationship between microstructure and properties.
- Academic research: Metallographic techniques are widely used in academic research to investigate a wide range of topics, from phase transformations to the effects of deformation on microstructure.

Final Thoughts
Metallographic polishing machines have become essential equipment for laboratories and industries involved in materials analysis. The lab consumables supplier Scopelab gives you the introduction and includes a diverse range of machine types, from single-wheel to fully automatic models, ensuring that there is a suitable solution for every application. By understanding the working principles and applications of these machines, you can effectively prepare metal samples for microscopic examination, gaining valuable insights into material properties and performance.