Cutting is the first and most important step in sample preparation. To cut the samples, the metallurgical sample cutting machine uses a resin cut-off wheel that rotates quickly. It includes a cooling system to prevent the sample from burning. It is widely used in metallurgical laboratories for cutting a variety of samples and is simple to use and maintain. When used with proper training and safety protocols, metallurgical sample cutting machines are easy to use and safe. When selecting a machine, consider factors such as ease of use, maintenance requirements, and safety features. Understanding the typical applications allows you to choose a machine that meets your specific requirements for producing high-quality samples for material analysis. This guide examines key factors to consider when purchasing a metallurgical sample cutting machine, with a focus on usability, safety, and typical applications.
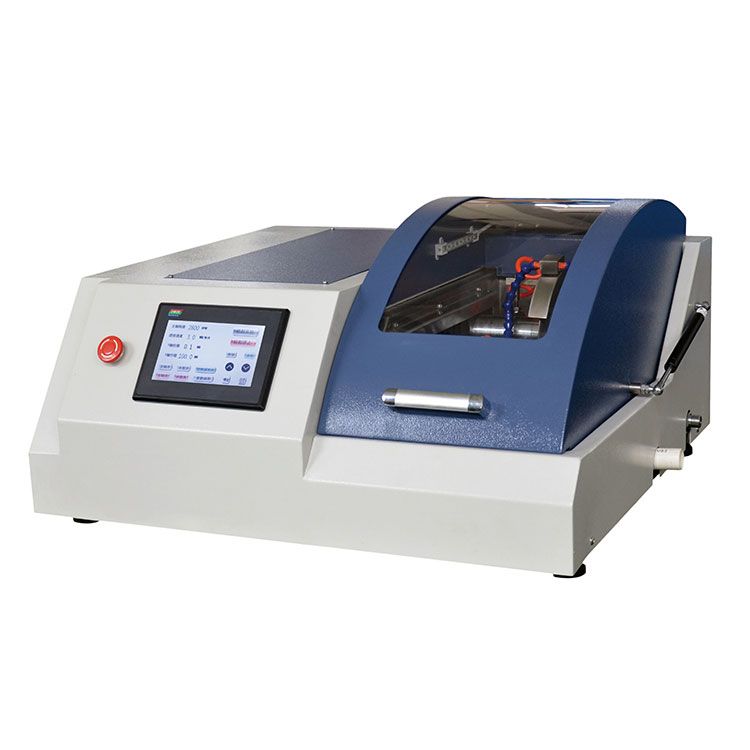
Is the Metallurgical Sample Cutting Machine Easy to Operate and Maintain?
The ease of operation and maintenance of a metallurgical sample cutting machine varies by model, but these machines are generally designed to be user-friendly. Here is a breakdown of what you can expect:
Ease of Operation
- Simple Controls: Most machines have user-friendly interfaces that include buttons, knobs, or touchscreens for speed control, cutting depth adjustment, and machine start/stop.
- Clear Visual Cues: Indicating lights or displays may indicate operational status, blade wear, or cooling system function.
- Minimal Training Required: A well-written user manual enables operators to learn basic cutting operations with minimal training.
Maintenance Considerations
- Blade Replacement: The most common maintenance task is to replace the cutting blades. This is usually a simple process that is outlined in the user manual. Blade sizes and materials vary depending on the application.
- Cooling System Upkeep: Some machines require periodic coolant refilling. Other models may necessitate filter changes for the cooling system.
- General Cleaning: To ensure functionality and safety, the machine must be cleaned of debris and metal chips regularly.
Factors Affecting Ease of Use and Maintenance
- Machine Complexity: More advanced models with features such as automatic cutting cycles or programmable settings may necessitate slightly more operator training.
- Manufacturer Design: Some companies prioritize user-friendly features in their machine design, making them easier to use and maintain. Look for features like easy access to components and self-diagnostic systems.
Metallurgical sample cutting machines are designed for use in laboratory settings, and usability is a key consideration for manufacturers. While some advanced features may necessitate additional training, most models can be operated and maintained with little difficulty by people with basic technical skills. For the most user-friendly experience, consider the control panel layout, ease of blade replacement, and the availability of clear user manuals and manufacturer support.
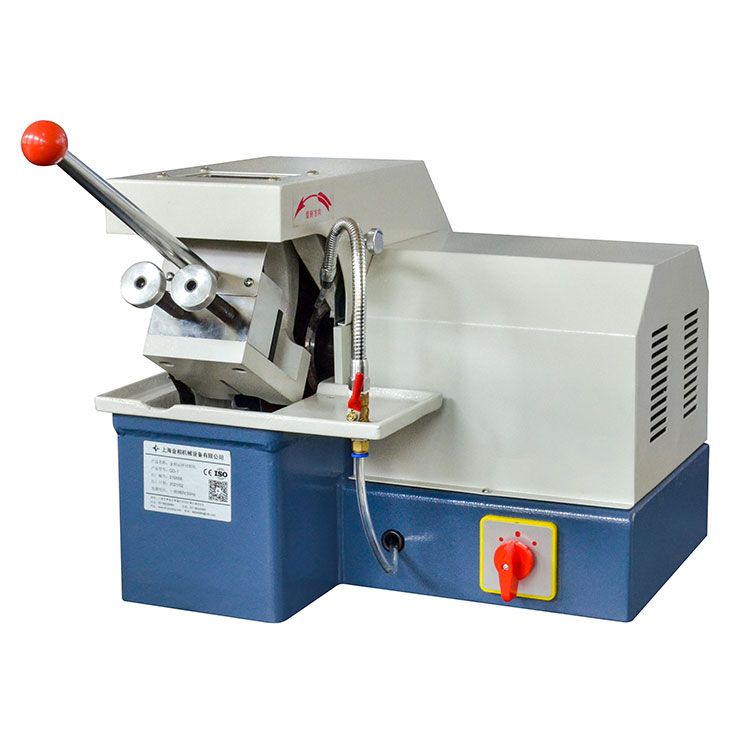
What Safety Features Does the Metallurgical Sample Cutting Machine Have?
Metallurgical sample cutting machines operate with sharp blades, rotating parts, and the possibility of sparks and debris. To ensure operator safety, these machines are equipped with several key features:
Protective Enclosures
- Machine Guards: An enclosed cutting chamber with a door or lid is a key safety feature. This avoids accidental contact with the cutting blade and flying debris during operation. The interlock system ensures that the machine will not start unless the enclosure is closed.
- Splash Guards: Some machines may have splash guards around the cutting area to contain coolant or lubricant sprays.
Interlock Systems
- Door Interlock: As previously stated, the most common interlock prevents the machine from starting while the cutting chamber door is open. This ensures that the operator’s hands are safely out of the way before proceeding.
- Emergency Stop Button: In the event of an emergency, the operator can quickly shut down the machine by pressing a prominently placed emergency stop button.
Additional Safety Features
- Foot Pedal Operation: Some models may include a foot pedal to control cutting initiation, freeing up the operator’s hands for more efficient sample handling.
- Blade Guards: Specific blade designs may include guards that partially cover the cutting edge to provide additional protection during blade replacement or sample loading.
- Visual and Audible Alerts: Machines may include warning lights or sounds to indicate operational status, low coolant levels, or other potential safety issues.
Remember that adhering to proper safety protocols is critical when operating any machinery. Always refer to the user manual for specific safety instructions for your particular machine model. Wear appropriate personal protective equipment (PPE), such as safety glasses, gloves, and ear protection. Never get into the cutting chamber while the machine is running. Ensure adequate ventilation to remove dust and fumes produced during cutting. Regularly check the machine for signs of damage or malfunction. Only trained personnel should use the machine.
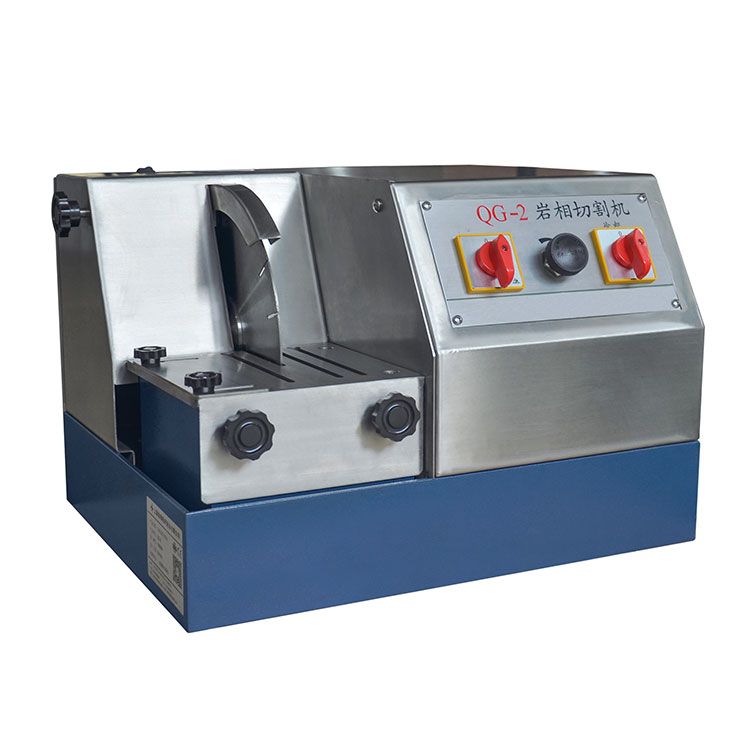
What Are the Typical Applications for Metallurgical Sample Cutting Machines?
Metallurgical sample cutting machines are extremely useful in a variety of fields that require material analysis. Such as the Scopelab QG-3 metallurgical sample cutting machine is widely used in Metallurgical laboratories, research institutions, colleges and universities, the metallurgical industry, shipbuilding, aerospace, and other heavy industries. Here are some of the typical applications for metallurgical sample cutting machines.
Metallography
This is the main application for these machines. Metallurgical analysis investigates the microstructure of metals and alloys. Samples are cut from components for further processing and examination under a microscope. The precise cuts cause minimal damage to the microstructure, allowing for accurate analysis of grain size, inclusions, and other characteristics.
Failure Analysis
When a metal component fails, a metallurgical sample cutting machine extracts sections of the failed part. These sections are then examined to determine the source of failure. This information is critical for future improvements to material selection, design, and manufacturing processes.
Quality Control
Metallurgical sample cutting machines are used in manufacturing processes to extract samples from production runs for quality control testing. These samples can then be subjected to various tests, such as tensile testing or hardness testing, to ensure that they have the desired material properties.
Research and Development
Creating new materials or optimizing existing ones frequently requires extensive testing and analysis. Metallurgical sample cutting machines play an important role in this process because they prepare samples of new materials for characterization and property evaluation.
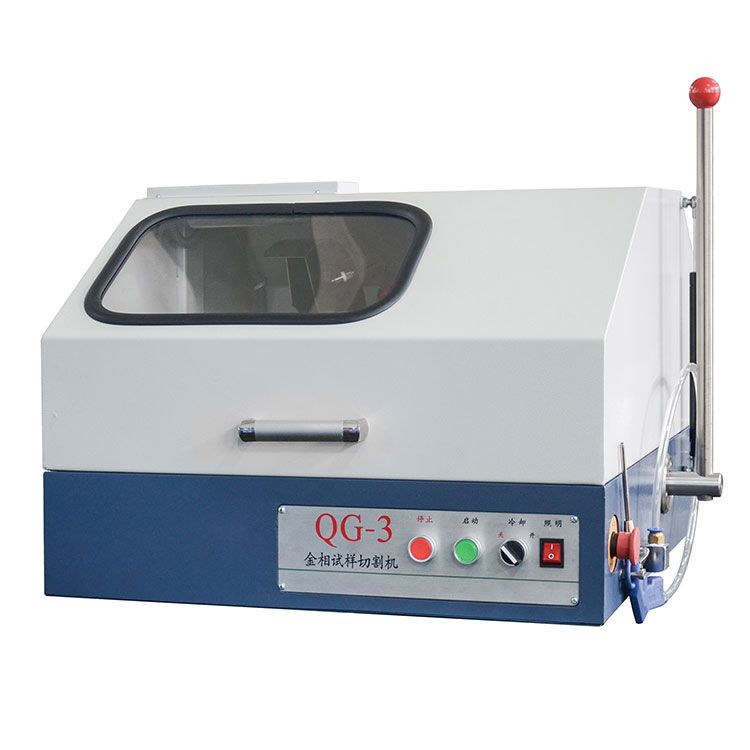
Conclusion
Metallurgical sample cutting machines are essential tools in material science and engineering. They enable the preparation of high-quality samples for analysis, revealing critical information about the microstructure and properties of various materials. You can choose a metallurgical sample cutting machine that optimizes your workflow and ensures the integrity of your material analysis by prioritizing user-friendly features, and robust safety measures, and taking into account your specific application requirements. Remember to consult the user manual and follow proper safety protocols to ensure safe and efficient operation. With the right tools and techniques, you can discover a wealth of information about the materials that shape our world. Chongqing Scope Instrument Co., Ltd. specializes in the supply of laboratory and medical training instruments and equipment. If you need metallurgical sample cutting machines, please contact us.