In today’s manufacturing environment, maintaining material quality and consistency is critical. Brinell hardness testing is a well-established method for measuring a material’s indentation hardness, which provides useful information about its mechanical properties. Traditional Brinell testers, while reliable, are time-consuming, subject to human error, and lack the data storage capabilities required for modern quality control practices.
This article delves into the world of digital Brinell hardness testers, explaining how they overcome these limitations and significantly improve your hardness testing capabilities. We’ll look at the key differences between digital and traditional testers, how easy they are to use, and any special calibration and maintenance requirements for digital models. By the end of this article, you’ll be able to understand the benefits of digital Brinell hardness testers and decide whether they’re the best fit for your hardness testing requirements.
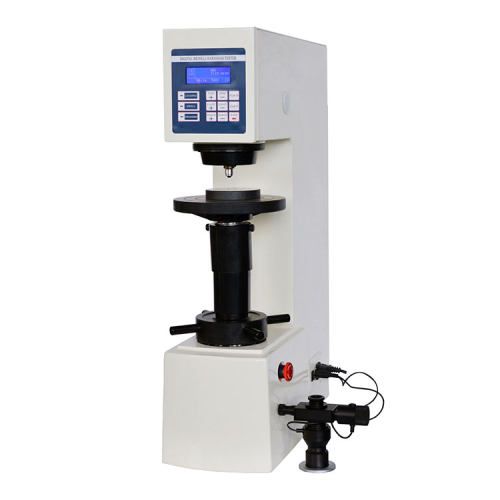
What Are the Differences Between Digital Brinell Hardness Testers and Traditional Brinell Hardness Testers?
Feature | Digital Brinell Hardness Tester | Traditional Brinell Hardness Tester |
Load application | Automatic. Digital Brinell hardness testers apply the load to the indenter via an electronic system. This ensures that the load is applied precisely and uniformly. | Manual. Traditional Brinell hardness testers apply the load manually, which can lead to measurement errors. |
Measurement | Electronic. Digital Brinell hardness testers measure the indentation with an electronic sensor. This provides a more precise measurement than the optical method used in conventional Brinell hardness testers. | Optical. |
Data storage | Electronic. Test results can be saved electronically for easy retrieval and analysis. | Manual. Test results are manually recorded, making them more difficult to retrieve and analyze. |
Accuracy | Higher. Digital Brinell hardness testers have higher accuracy than traditional Brinell hardness testers. This is caused by the use of electronic systems for load application and measurement. | Lower. |
Ease of use | Easier. Digital Brinell hardness testers are simpler to operate than traditional Brinell hardness testers. This is because they have user-friendly interfaces and frequently automate tasks such as load application and measurement. | More difficult. |
Digital Brinell hardness testers have several advantages over traditional Brinell hardness testers, including improved accuracy, easier data storage and retrieval, and shorter testing times.
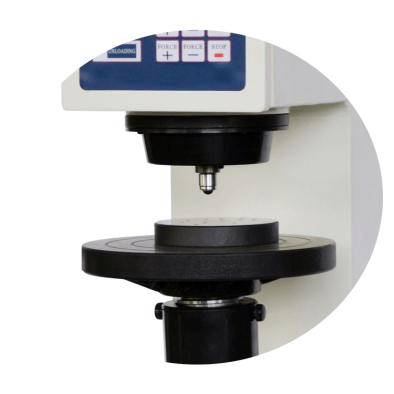
Is the Digital Brinell Hardness Tester Easy to Operate?
Yes, Digital Brinell Hardness Testers are generally considered easier to operate than traditional Brinell testers. Here’s a breakdown of why:
User-friendly Interfaces
Digital testers have clear digital displays that display critical information such as test parameters, force applied, and hardness measurements. This eliminates the need for manual calculations and reduces the possibility of errors when reading analog dials on traditional models. Many testers have intuitive menus that walk you through the testing process step by step. Simple button presses or touchscreens are frequently used for basic operations, reducing the need for intricate manual adjustments.
Automation Features
Digital testers can automatically apply the necessary test load, ensuring consistent and accurate pressure on the material. This eliminates the variability associated with manual load application in traditional testers. When the load is applied, the tester measures the indentation depth electronically. This eliminates the need for manual measurement using a microscope, which is time-consuming and potentially error-prone in traditional testers. Many digital testers can electronically save test results, such as hardness values, test parameters, and dates/times. This information can then be exported to a computer for further processing and report generation. This saves time and improves record-keeping when compared to traditional testers, which use manual data recording.
Additional Features that Enhance Ease of Use
Some models include calibration reminders or prompts to ensure the tester’s accuracy. This eliminates the need to remember calibration schedules, which can be critical for ensuring test integrity. If something goes wrong during the test, digital testers may display error messages or provide feedback, allowing you to quickly identify and resolve issues.
Overall, digital Brinell testers are intended to be user-friendly and accessible to operators of various levels of experience. To make testing easier, look for models with clear displays, intuitive menus, and automatic features. To get a sense of how your chosen tester works, consult user manuals or watch manufacturer videos.

Are There Any Special Calibration and Maintenance for Digital Brinell Hardness Testers?
Both digital and traditional Brinell hardness testers require calibration and maintenance to produce accurate and consistent results. However, there are some variations in how they are handled:
Calibration
Both digital and traditional Brinell hardness testers require regular calibration to ensure accuracy in measuring material hardness. This calibration process is typically performed at predetermined intervals, often on an annual basis. However, the actual frequency can vary depending on several factors.
- Manufacturer Recommendations: Different manufacturers may have their own recommended calibration schedules based on the model and its components. These recommendations should be the primary consideration when determining calibration frequency.
- Usage Frequency: The more frequently you use the Brinell hardness tester, the more calibration may be required. Heavy use can cause wear and tear, which can compromise accuracy.
- Industry Standards: Certain industries may have regulations or standards in place regarding the frequency of Brinell hardness tester calibration. Adherence to these standards ensures compliance and data integrity.
Following a proper calibration schedule ensures that both digital and traditional Brinell hardness testers provide accurate and consistent hardness measurements.
Process
Calibration of traditional Brinell hardness testers typically involves using certified test blocks with known hardness levels. The tester is used to determine the hardness of the blocks and compare the results to the certified values. Any discrepancies necessitate adjustments to the tester. Calibration procedures for digital Brinell hardness testers may include software adjustments and the use of specialized calibration equipment provided by the manufacturer or a certified calibration service. Some advanced models may include user-accessible calibration routines.
Maintenance
General upkeep is similar. Both testers require regular cleaning and inspection to remove dirt, debris, and grease as needed. Following manufacturer recommendations for maintenance schedules and procedures is critical. Digital testers may necessitate more attention to the electronic components to ensure proper connections and functionality. Some models may require periodic software updates from the manufacturer to maintain accuracy and functionality.
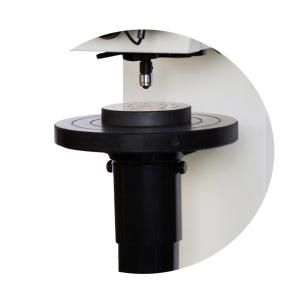
Conclusion
Digital Brinell hardness testers mark a significant advancement in material testing technology. Their superior accuracy, efficiency, and data management capabilities provide a compelling alternative to traditional models. Whether you want to streamline testing processes, reduce human error, or improve data analysis for quality control, digital Brinell testers can provide a significant advantage. While both digital and traditional testers require calibration and maintenance, digital models may necessitate slightly more complicated procedures due to their electronic and software components. However, with proper care and adherence to manufacturer recommendations, they can provide a dependable and long-lasting solution for your hardness testing requirements. If you want to improve the accuracy, efficiency, and overall quality of your hardness testing procedures, you should seriously consider using a digital Brinell hardness tester (such as MHB-3000 or XHB-3000 provided by Brinell hardness tester supplier Scopelab is a good choice). By choosing this advanced technology, you can ensure consistent, reliable data that empowers confident decision-making in your material selection and manufacturing processes.