Metallographic microscopes are essential tools in industrial inspection, particularly for analyzing material structures and ensuring quality in manufacturing processes. There are two primary configurations of metallographic microscopes exist: upright (or conventional) and inverted. Both serve the fundamental purpose of magnifying and illuminating a prepared sample for observation and analysis. However, their distinct designs lead to different strengths and weaknesses, making one configuration potentially more suitable than the other depending on the specific industrial inspection requirements. This article aims to delve into the technical characteristics, industrial applications, and considerations for choosing between upright and inverted metallographic microscopes.
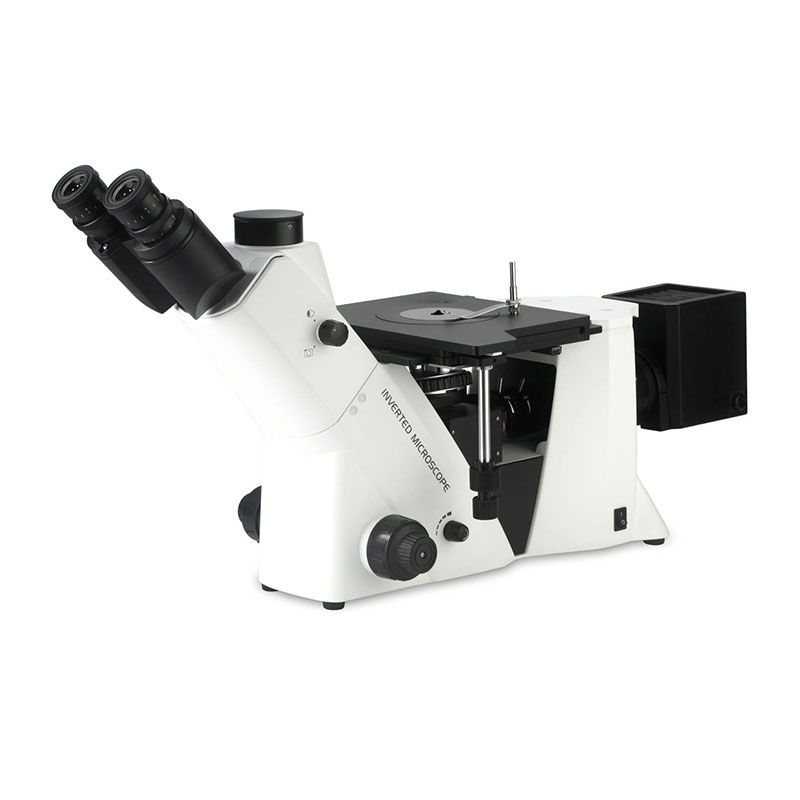
Requirements of Industrial Inspection
Industrial inspection demands efficient, reliable, and accurate material analysis. Several core requirements drive the selection of appropriate metallographic equipment.
- Firstly, sample compatibility is paramount. Industrial samples often vary significantly in size, shape, and weight. The microscope must be able to accommodate these diverse specimens without requiring extensive or potentially damaging preparation.
- Secondly, detection efficiency is crucial for high-throughput quality control. The speed and ease with which samples can be mounted, focused, and analyzed directly impact productivity.
- Thirdly, image quality and clarity are non-negotiable for accurate identification of microstructural features and defects. High resolution and contrast are essential for reliable analysis.
- Finally, versatility and expandability are increasingly important. The ability to perform various imaging techniques (e.g., brightfield, darkfield, polarized light, DIC) and integrate with analytical tools (e.g., image analysis software, microhardness testers) enhances the scope and value of the inspection process.
Meeting these core requirements effectively ensures the quality and consistency of manufactured goods.
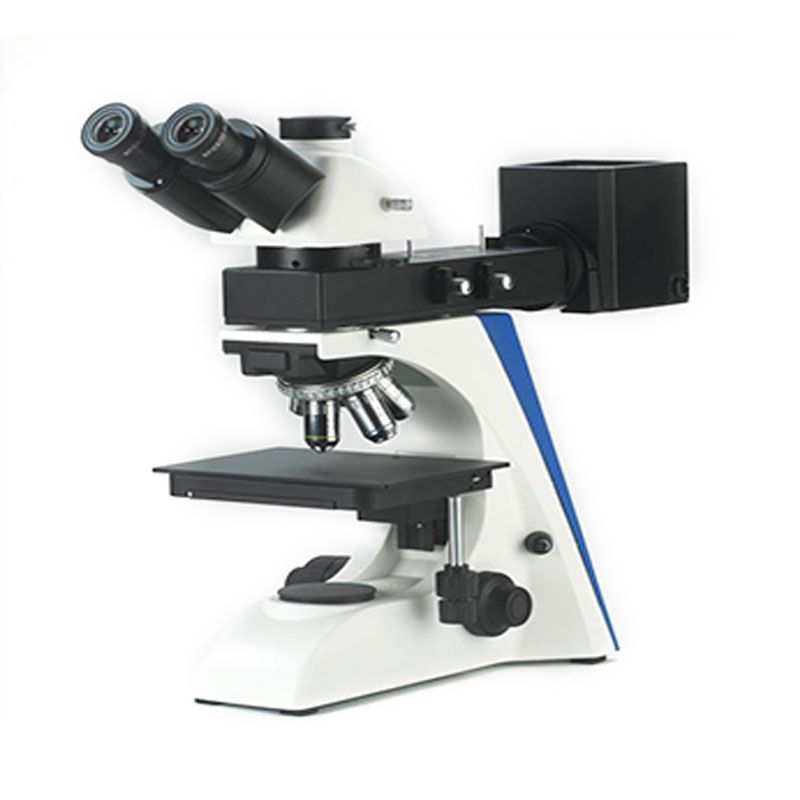
Technical Features Comparison
The technical differences between upright and inverted metallographic microscopes significantly influence their performance in industrial contexts. Below is a detailed comparison:
Feature | Upright Metallographic Microscope | Inverted Metallographic Microscope |
Optical Path | Objective lens is positioned above the sample, light source typically above. | Objective lens is positioned below the sample, light source typically below. |
Sample Compatibility | Generally better for smaller, regularly shaped, and well-prepared samples. Can struggle with large or irregularly shaped samples due to stability and focusing challenges. | Excellent for large, heavy, and irregularly shaped samples. The flat, polished surface rests stably on the stage, simplifying focusing. |
Detection Efficiency | Sample mounting and leveling can be more time-consuming for irregular samples. Focusing may require more adjustments for uneven surfaces. | Sample placement is generally faster and simpler, especially for flat, polished surfaces. Focusing is more consistent as the polished surface is always perpendicular to the optical axis. |
Expandability | Wide range of accessories available, including stages for various sample sizes and manipulation. Integration with microhardness testers can be more complex due to sample orientation. | Well-suited for integration with microhardness testers as the sample remains stable and accessible after imaging. Specialized stages for large samples are readily available. |
Suitability for Industrial Inspection
Upright Microscopes: Preferred for small, precise samples, offering detailed imaging with high magnification and advanced analytical features.
Inverted Microscopes: Ideal for bulkier, complex samples due to their ability to inspect without extensive preparation.
Each microscope type provides unique advantages. The choice depends on sample characteristics and inspection priorities.
Industry Application Case Analysis
To illustrate the practical use of upright and inverted microscopes, the following table summarizes some typical applications:
Industry | Application | Microscope Type Preference | Rationale |
Automotive | Inspection of engine blocks, crankshafts, gears for microstructure and defects. | Inverted | Large, heavy components are easily accommodated. Integration with microhardness testing for surface treatment evaluation is common. |
Aerospace | Analysis of turbine blades, airframe components for grain structure and fatigue cracks. | Both | Smaller, precisely machined parts may be suitable for upright microscopes. Larger forgings and castings benefit from the stability of inverted designs. |
Electronics | Examination of solder joints, microelectronic packaging for defects and material integrity. | Upright | Smaller, well-prepared samples are typical. High magnification and specialized illumination techniques are often required. |
Steel Manufacturing | Quality control of steel sheets, bars, and welds for inclusions, grain size, and phase transformations. | Inverted | Large, often heavy samples are common. Ease of handling and stable observation are crucial for routine quality checks. |
Medical Devices | Analysis of implant materials, surgical instruments for biocompatibility and manufacturing defects. | Upright | Smaller, precisely prepared samples are typical. Focus on high-resolution imaging and specific material characterization. |
Both microscope types have proven their value across various industries. Choosing the right one often hinges on balancing sample size and inspection precision.
When to Choose an Upright or Inverted Metallographic Microscope
The decision of whether to choose an upright or an inverted metallographic microscope for industrial inspection hinges on several key factors related to the samples being examined and the specific requirements of the analysis.
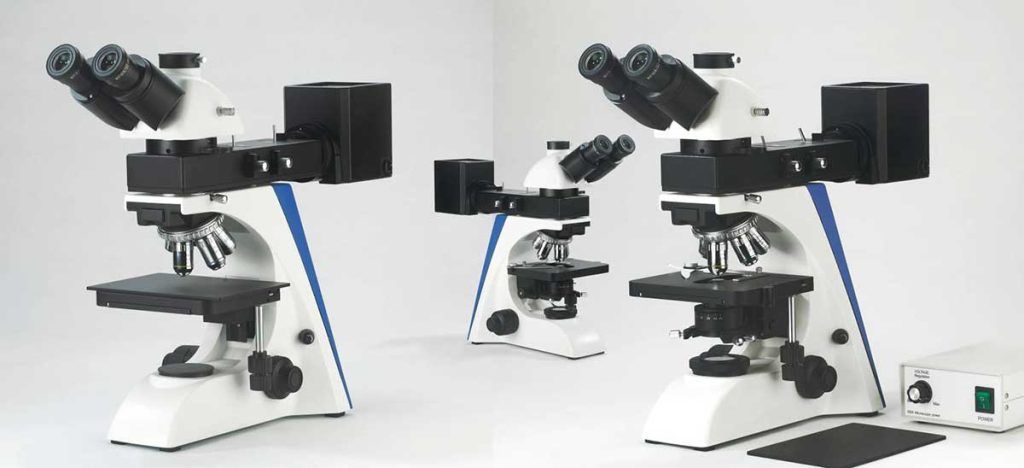
Choose an Upright Metallographic Microscope when:
- Analyzing smaller, regularly shaped, and easily manageable samples: If your typical samples are relatively small and can be easily oriented with the surface of interest facing downwards, an upright microscope can be a versatile and cost-effective solution.
- Requiring a wide range of specialized illumination techniques: Upright microscopes often offer a broader array of readily available illumination options and accessories for specific contrast enhancement techniques.
- The primary focus is on high magnification and resolution for detailed examination of well-prepared surfaces: For intricate microstructural analysis of smaller areas, an upright microscope can provide excellent image quality.
- Integration with certain analytical tools (other than microhardness testing) is the priority: While integration with microhardness testers can be more complex, upright microscopes can be readily adapted for other specialized analyses.
Choose an Inverted Metallographic Microscope when:
- Dealing with large, heavy, or irregularly shaped samples: The stability and ease of handling large and awkward samples on an inverted stage are significant advantages in many industrial settings.
- Routine inspection of a high volume of samples with flat, polished surfaces is required: The simplified sample placement and consistent focusing of an inverted microscope enhance efficiency in high-throughput quality control.
- Integration with a microhardness tester is a crucial requirement: The stable, upward-facing sample on an inverted microscope is ideal for performing microhardness indentations directly after microscopic observation.
- Maintaining focus on the prepared surface is critical, regardless of the overall sample geometry: The inverted design ensures that the focal plane remains parallel to the polished surface, even if the sample itself is uneven.
In conclusion, both upright and inverted metallographic microscopes are powerful tools for industrial inspection. Understanding their fundamental design differences and the specific needs of the application will guide the selection process, ensuring optimal efficiency, accuracy, and reliability in material analysis and quality control. Careful consideration of sample characteristics, throughput requirements, and the need for integrated analytical techniques will ultimately determine which configuration is the more suitable choice for a given industrial setting.